SPEE3D’S Cold Spray AM Tech Prints Metal Parts In Sub-Zero Temps
SPEE3D was selected to participate in developing, demonstrating, and testing their cold spray metal additive manufacturing (CSAM) equipment, company reports.
December 17, 2024
SPEE3D reports that its XSPEE3D system is able to operate in a subzero environment and produce parts with comparable material properties to the parts produced in a laboratory environment. SPEE3D was selected to participate in developing, demonstrating, and testing their cold spray metal additive manufacturing (CSAM) equipment, along with partners from the New Jersey Institute of Technology (NJIT) COMET Project and Philips Federal, as part of the Office of the Secretary of Defense Manufacturing Technology's Point of Need Challenge (PON).
The PON project was managed by LIFT, the Detroit-based Department of Defense Manufacturing Innovation Institute, and it concluded that the XSPEE3D system is well-suited to support the DOD's goal of expanding expeditionary manufacturing capabilities in extreme cold weather environments for battle damage repair and large metal component production, SPEE3D reports.
“The positive results of the Point of Need Challenge demonstrate that the XSPEE3D can print metal parts from anywhere—and in any weather conditions—with the same successful outcomes,” says Byron Kennedy, CEO of SPEE3D. “Previously, we partnered with the Australian Army and showed that our technology can print parts in the extremely hot, rugged Australian bush. Now, we're proving that we can also successfully print parts in the coldest of environments, helping to support the DOD's goal of expanding manufacturing capabilities in austere environments.”
The U.S. Army's Cold Region's Research and Engineering Laboratory (CRREL) hosted the PON challenge in Hanover, NH, in late 2023. The program showcased technologies that will keep service members combat-effective in extreme temperatures and exhibited systems that can be deployed in a cold weather environment. These systems close supply chain gaps and enable warfighters to manufacture and use critical equipment on demand in the harshest environments.
“The Point of Need challenge winners have proven to be champions of research and innovation and are helping drive the United States military's technological advantage through the latest in advanced materials and manufacturing process technologies,” says Noel Mack, chief technology officer, LIFT. Through SPEE3D’s innovative work, they have proven that not only does the technology to support the warfighter exists, but it can be placed closer to where they need it to achieve their missions successfully.”
Sources: Press materials received from the company and additional information gleaned from the company’s website.
Subscribe to our FREE magazine,
FREE email newsletters or both!About the Author

DE’s editors contribute news and new product announcements to Digital Engineering.
Press releases may be sent to them via DE-Editors@digitaleng.news.
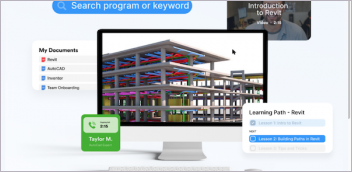
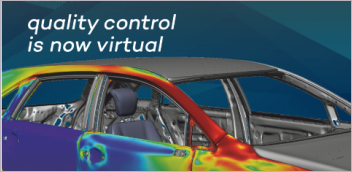
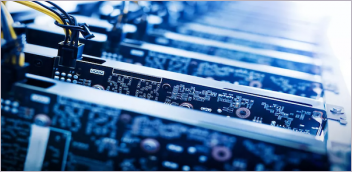
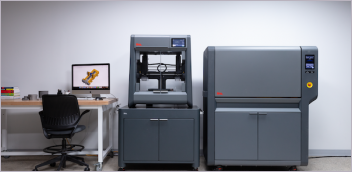