
3D printing filament materials provider Polymaker showcases the range of colors available. Image by Kenneth Wong, DE 24/7
Rapid + TCT 2024: AM Industry Courts New Users with Easy, Intelligent Software
3D printing industry seeks new ways to expand adoption
Latest News
July 3, 2024
Last week, hardware and software makers in Additive Manufacturing (AM) assembled at the Los Angeles Convention center for Rapid + TCT, the 30-year-old annual conference organized by The Society of Manufacturing Engineers (SME) and TCT magazine. During the Executive Perspectives panels at the show, a mix of optimism, anxiety, and impatience bubbled up.
The Mood of the Industry
Charlie Grace, Chief Commercial Officer, Nikon SLM, said, “It's been an extraordinary year, exceeding expectations.” Marie Langer, CEO of EOS, said, “These are exciting times, but we need to be patient.” Yoav Zeif, CEO, Stratasys, said, “I have one big goal, which is adoption.”
For Yoav Stern, CEO of Nano Dimension, “This industry is definitely not where we thought it would be.” He revealed, “I've looked at about 350 companies over the last four years. ... None of the companies I looked at is making money yet. For the private companies that I don't know about, I'll give them the benefit of the doubt.”
While hardware makers are not generating profits, printing service providers are turning a profit, Stern said. “That is an abnormality that cannot continue,” he added. For him, consolidation is the path to growth. “You can't make money when you are too fractured,” he noted. Langer, however, countered that “coopetition and strategic partnerships” are the path to growth.
Savi Baveja, President of 3D Printing, HP, suggested, “We should jointly develop standards, jointly publish reports, and jointly market 3D printing. We all generally get along, so it shouldn’t be this hard.”
Between late 2023 and early 2024, Nano Dimension made numerous aggressive moves to acquire rival Stratasys, but was rebuffed. This week Nano Dimension and Desktop Metal jointly announced they plan to merge. Stern said, “Our combination with Desktop Metal is another step in Nano Dimension’s evolution to become the leader in digital manufacturing.”
Transportable Systems & Pellet-Based Printing
Typically critical parts are 3D-printed and shipped to the target site for installation, but Spee3D offers a different approach. It designs Cold Spray Additive Manufacturing systems that can be loaded into a container and towed to the destination for on-location printing.
Bryon Kennedy, CEO of Spee3D, explained, “Think of defense, mining, oil and gas, rail, and marine industries. They have large, expensive infrastructure, which they need to keep running. And what happens when a $50 part breaks? It may not be something complex, but it may be crucial to the particular application. if that infrastructure is down, it might be costing them a million dollars an hour. So they'll either stock a whole bunch of spare parts, or they'll fly them in. For them, it's not unusual to spend $100,000 to bring in a $50 part.”
For such customers, a movable, transportable system makes more sense to address their urgent needs. Spee3D is also reconfiguring its systems as LightSPEE3D, a permanently installed onsite printing solution.
At the show, 3D Systems introduced the Titan EXT 800, a high-speed industrial system that uses pellet extrusion. The company said its system could produce up to 10X the output of competing FFF and FDM printers. “Thermoplastic pellet feedstocks reduce material costs up to 10X compared to filaments. The EXT 800 is also our most affordable pellet extrusion system, accelerating your path to positive ROI,” according to 3D Systems.
ChatGPT for Print Prep
On the show floor, Ai Build showcased version 2.0 of its print prep software. The software allows you to upload a part, slice it, optimize it, and simulate and monitor the build process. With ChatGPT-style UI that allows you to enter your command in natural language, the software is especially suited for novices, according to the company. Michail Desyllas, Cofounder and COO, Ai Build, said, “This is very useful for people who are starting their AM journey. AM requires highly trained people to control the process. [The software] for us is a way to accelerate and help the industry grow.”
Software is the Key to Adoption
The emergence of manufacturing-grade 3D printers was accompanied by the rise of DfAM (Design for AM) software. Such software allows design engineers to create parts with complex geometry and lattice structures that take advantage of AM's unique capabilities.
Harshil Goel, CEO and Founder, Dyndrite, said, “If someone is going to make a commitment to buy a large machine or make a major investment in buying lots of these machines, they want to get every efficiency or potential out of the hardware. And the way to do that is, in my opinion, through software.”
Jaideep Bangal, Director of Simulation and Manufacturing, Altair, said, “How does the engineer knows this is the perfect design for AM? How does he know this part is going to perform well? [Software] tools at Altair has helped design engineers to design the parts, and optimize the parts for AM.”
Warp-Adjusted Modeling, Printing from CAD
Warping is a regular feature of printed parts, partly due to the extreme heat in the melt pool and the powder depositing process. Some DfAM software vendors are now adding tools to automatically generate warp-compensated models. In software such as GrabCAD Print from Stratasys, “You can compare [the scanned printed part] to the original CAD file to figure out how much it has warped. Then you can counter-warp the part in the opposite direction, so when you print again, the part comes out how you want it,” explained Tim Crennen, Senior Applications Engineer, GoEngineer.
The method requires the use of digital scanners to capture the printed parts accurately, in order to identify the deviation from the original CAD file. On the show floor, Artec 3D and Hexagon demonstrated the workflow using their Artec Space Spider and Hexagon ALTASCAN.
Whereas STL and 3MF have been the standard file formats to send to printers, the DfAM software developers are now exploring ways to use the CAD file itself to print. While reliable, tessellated files such as STL and 3MF also increase the file size significantly, making the print process unwieldy.
Goel said, “You don't want to export your design as a mesh. Ideally, you want to just import the native CAD data [into the print prep software], slice it, and then send it to the machine.”
Software such as Materialise Magics allows you to work with both mesh and implicit files from nTop in the print process. Similarly, the latest version of nTop allows you to export parts into Autodesk Fusion as native files without meshing. While not yet widespread, such tools may be paving the way toward directly 3D printing from the CAD file itself.
For more, watch the video report above.
Subscribe to our FREE magazine,
FREE email newsletters or both!Latest News
About the Author

Kenneth Wong is Digital Engineering’s resident blogger and senior editor. Email him at kennethwong@digitaleng.news or share your thoughts on this article at digitaleng.news/facebook.
Follow DE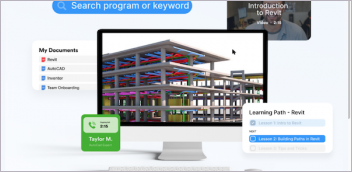
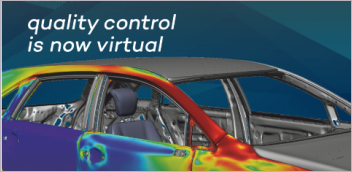
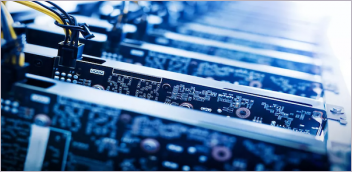
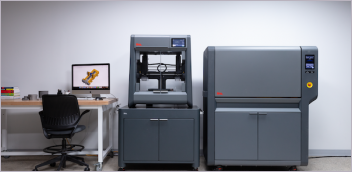