Latest News
March 22, 2022
MachineWorks Ltd, supplier of software components to the engineering industry, has released MachineWorks 8.4.
Headline enhancements include:
- computation of safe holder profiles;
- multiple simultaneous holder and tool collision checks;
- improved simulation performance through collision check buffering;
- extensions to design part comparison Render Query;
- enhanced analysis of intersect solids for bending simulation;
- new sectioned stock view;
- application-defined swept volumes; and
- computation of safe holder profiles.
Using this new method applications can determine the maximum safe profile that can be used to machine a particular toolpath without collisions. The resulting holder profile can be compared with available holders in a tool library, allowing the end user to choose a holder they know will not cause collisions during the cutting process, the company reports.
Multiple Tool Collision Checks
A new function has been added to compute multiple simultaneous collision checks between tools and holders and/or stocks and fixtures, allowing fast determination of safe access limits with a particular holder or combination.
The function is internally multithreaded to provide performance for toolpath generation and optimization algorithms, along with rapid path evaluation for CMM and Metrology inspection plans.
Improved Simulation Performance
This new option allows computation of collision checking to be deferred until required by the host application. This option improves performance for CMM and Metrology inspection applications.
Extensions to Design Part Comparison Analysis
The MachineWorks Render Query APIs have been extended, with respect to analyzing design part or target part comparison results.
The Render Query application programming interfaces (APIs) provide an optimized mechanism to decouple the graphical simulation from the geometric simulation, allowing tight integration of MachineWorks to external graphics environments or use in distributed deployments such as public and private clouds.
- Cut numbers are now available in render query updates.
- New APIs allow the Render Query analysis mesh to be serialised to disk.
- New filters are provided to specify which triangles are delivered by the Render Query update.
- A new API to provide direct export of analysis mesh distance information has been provided.
Enhanced Analysis of Intersect Solids
New API functions have been added to split and recombine the solids of intersection created between the in-process stock and swept-volume during a cutting operation.
Sources: Press materials received from the company and additional information gleaned from the company’s website.
More MachineWorks Coverage
Subscribe to our FREE magazine,
FREE email newsletters or both!Latest News
About the Author

DE’s editors contribute news and new product announcements to Digital Engineering.
Press releases may be sent to them via DE-Editors@digitaleng.news.
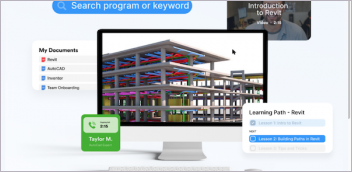
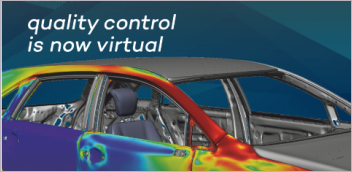
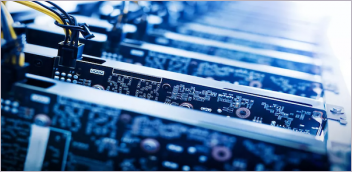
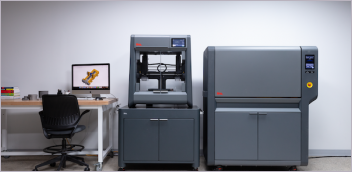