Latest News
November 14, 2018
Dear DE Reader:
NUMECA International is well known among CFD (computational fluid dynamics) mavens as a developer of toolsets with neat application-driven interfaces and features, integrated multidisciplinary capabilities as well as such characteristics as automatic full-hex meshing. They're also known for hitting the mark with users who have specific industrial requirements like automotive, hydro and marine, oil and gas, acoustics and turbomachinery. Today's Editor's Pick of the Week meshes together those last two.
NUMECA recently released version 8.1 of its FINE/Acoustics integrated simulation suite for aero-acoustics and vibro-acoustics projects. They report that they spent a lot of time making this toolset more robust and user-friendly. They also added more functions to the Python API (application programming interface) to extend scripting abilities. Still, the key new addition is a wizard for turbomachinery broadband and tonal noise analyses.
A little background: You can use FINE/Acoustics for your preliminary calculations as well as large-scale analyses. It has a host of solvers and methods that you can bring to bear on your assignments. For example, FEM (finite element method) and BEM (boundary element method) for propagation analyses or FW-H (Ffowcs Williams-Hawkings) for radiation analyses. You can import solutions in various industry-standard formats and do fluid-structure couplings by importing structural modes from, say, Abaqus or NASTRAN and so on.
NUMECA describes FINE/Acoustics version 8.1's new Turbomachinery Wizard as intended to help you predict tonal and broadband noise for turbomachinery projects. It uses solutions generated by the company's FINE/Turbo integrated environment for turbomachinery analysis as well as its FINE/Open with OpenLabs integrated multiphysics CFD environment.
The Turbomachinery Wizard works by letting you set up, run and post-process aero-acoustic analyses of tonal and broadband noise for turbomachinery configurations (axial, radial or mixed-flow) with what seems like great ease backed by a lot of automation.
Great ease means minimal user input: The basic workflow appears to be: import the CFD results, define the turbomachinery configuration (axial or centrifugal), pick the analysis type and let it rip. FINE/Acoustics then automatically meshes and runs the noise propagation analyses. That simplicity should help make life a tad easier as well as reduce design cycle times and costs.
You can learn more about FINE/Acoustics version 8.1 from today's main write-up, which includes a lengthy list of validation cases on academic and industrial configurations reported by NUMECA. The link at the end of today's main write-up takes you to the full skinny on the FINE/Acoustics analysis environment.
Thanks, Pal. – Lockwood
Anthony J. Lockwood
Editor at Large, DE
Subscribe to our FREE magazine,
FREE email newsletters or both!Latest News
About the Author

Anthony J. Lockwood is Digital Engineering’s founding editor. He is now retired. Contact him via de-editors@digitaleng.news.
Follow DERelated Topics
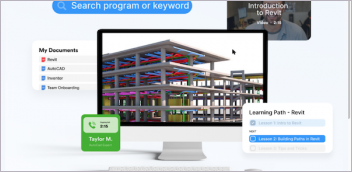
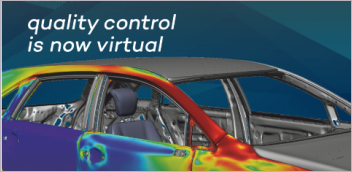
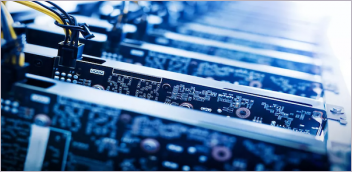
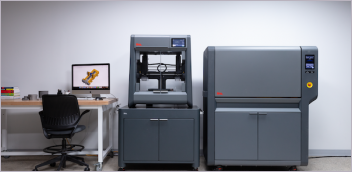