Design & Simulation Summit: Artificial Intelligence and Simulation
At the annual DE virtual event, industry experts debated the role of AI and machine learning, and provided guidance on simulation-led design, digital twins, additive manufacturing, and more

The Digital Engineering Design & Simulation Summit took place Oct. 31, and featured a keynote panel on AI in simulation.
Latest News
November 8, 2024
Is your AI hallucinating? That was one of the questions posed to a panel of artificial intelligence and simulation experts at the 2024 Digital Engineering Design & Simulation Summit, a virtual conference held on Oct. 31. During the live keynote panel, titled “Is Your CFD Hallucinating? Unpacking the Opportunities and Challenges of AI for Simulation,” attendees learned about current and possible future uses of AI in simulation workflows.
Astrid Walle, turbo machinery engineer Siemens Energy, said that hallucination issues boil down to the data used to train the model. She gave an example of a car manufacturer training a model on the pressure of airflow on the surface of a vehicle design, but only using data from vehicles of a certain size. “When you present a new model of car, you won’t see the pressure distribution because the model has no clue where it would be,” she said. “You need to be able to look at the results and decide whether they make sense or not.”
Panelist Sandeepak Natu, executive consultant at CIMData began his presentation with a quick industry overview, noting that the simulation analysis market has reached $10 billion, and is growing at about a 9% CAGR, with broader adoption of simulation across the product lifecycle and use of more model-based systems, multiphysics, digital twins – and AI. “There is a confluence of physics simulation and AI and ML techniques,” he said.
Taking note of recent merger and acquisition activity in the market, he added that the deals are getting bigger (Siemens acquiring Altair for $10 billion, as an example) and that there is a lot of activity on the venture funding side for smaller companies. Adoption of machine learning and AI is helping to fuel this interest.
According to Walle, one potential stumbling block is just the ability to manage the large amounts of data necessary for this next-level simulation. Right now, Siemens energy is monitoring and acquiring data from hundreds of turbines at customer sites. That data could potentially be used to train AI models to help guide new designs.
“That’s what I’m interested in with turbine design,” Walle says. “It’s about having this assistant to get to new designs, and it would be great to get to the goal of predictive machine learning.”
Alexander Lavin, founder and CEO of Pasteur Labs, took an even more forward-thinking view, and said that AI can allow a reshaping of the software stack for digital engineering, and that current AI-simulation offerings are not as ambitious as they could be.
As far as concerns around AI and machine learning accuracy in simulation, Walle says it will depend on data quality. “It depends on the data and what the technology is used for, and it depends on best practice, which I feel we need to develop now for this new technology. We need to figure out the benchmarks so we can come up with the same kind of best practices that we did for simulation, like mesh resolution studies.”
Sandeep at CIMData reinforced that standards will be important. “Physics solvers have gone through a large amount of validation and testing, and no manufacturer allows installation of a new version of that software unless it complies with that level of rigorous testing,” he said. “We need to be careful to develop similar methods for small models and large models. What governance mechanism will they have?”
Asked how AI-powered simulation might change the role of the engineer, Lavin clarified that ChatGPT-style or token-based systems are not what we should be focusing on. His company is focused on creating modular, asynchronous workflows. “We are interested in reshaping workflows. That is how we see machine learning and AI.”
To watch the on-demand video of the keynote panel, register here.
The Benefits of Simulation-Driven Design
In the design track, “How to Make Simulation-Driven Design a Strategic Advantage for Your Company,” sponsored by COMSOL and TotalCAE, Consultant Mark Meili, kicked off the session with some what-if questions for doing design better at your company:
- What if you could obtain deep insights without physical prototypes and learn in hours versus weeks?
- What if you could reduce the cost of what you manufacture with equal or potentially better performance than today?
- What if your organization was 30% to 50% more productive and 50% faster to market with new initiatives?
- And his biggest what-if: What if your finance department and business leadership saw you as a strategic advantage to your company?
Meili, who is retired from 35+ years at P&G, where he was responsible for modeling and simulation strategy and delivery as a way to make money for the company, among other tasks, discussed digital technologies as a business strategy, specifically how to build and carry out a strategy to keep you ahead of competition.
“One thing I learned [from his career], both good and bad, is that digital work processes are inherently disruptive to established companies. For those of you who work for startups and you’ve always done it this way, you accept that that’s the way it is.
“But for established companies that have ways of doing things, moving to digital work processes is disruptive. If you’re going to be disruptive in a constructive way, you have to be strategic,” he says, crediting his work in this area to efforts accomplished by the ASSESS Initiative and his 20+ years of personal experience.
“Business strategic value doesn’t just happen. It requires intent,” according to Meili. “You have to be purposeful to obtain that value.”
Meili shares three aspects to attaining value for your business:
- A desire to be strategic/maximize business impact
- Document work and partner with finance
- Strategic communication of intent and results
There’s not a one-size-fits-all for articulating value, according to Meili, but there are common themes.
He offered 5 ways to quantify value to drive business interest:
- Cost reduction of the item being manufactured.
- Lower development costs
- Speed of learning
- Improved quality and reduced warranty costs
- Improved safety and regulatory compliance
He further explored each of the points made with specific examples.
For more strategies and to listen to the entire on-demand session, click here.
Putting the Digital Twin to Work for your Business
Teresa Alberts, CEO of Switzerland-based ITficient, led the DE Design & Simulation Summit Digital Twin track, “Applications and Benefits of Digital Twins for the Manufacturing Industry,” sponsored by platinum sponsor nTop.
ITficient offers digital twin infrastructure and simulation services. The company and its partner services operate as a point of contact for deploying digital twins, according to Alberts.
During her talk, Alberts offered real-world case studies of digital twin use, but began by defining digital twins according to several outside sources including Digital Twin Consortium’s definition:
Digital Twins are motivated by outcomes, driven by use cases, powered by integration, built on data, enhanced by physics, guided by domain knowledge, and implemented in dependable and trustworthy IT/OT/ET systems.
“You can pick which one you like, but in the end, it’s a mix of everything,” Albert says. “A digital twin consists of data- and or physics-based models, integrates industry-specific guidelines/algorithms, and leverages existing experience and specialized expertise,” Alberts says.
Alberts shared market trends, mentioning the predictive maintenance segment is expected to hold the largest share of the digital twin market from 2023-2028. Additionally, findings from Gartner estimate that by 2027, over 40% of large companies globally will use digital twins to boost revenue.
Being from Switzerland, Alberts cited key reasons that Swiss SMEs use digital twins: to increase efficiency (72%), build competitive advantage (64%), to meet customer requirements (44%), and identify new business models (44%), citing ZHAW School of Engineering statistics.
Alberts then delved into use cases, providing digital twin best practices.
The first use case was Verbund (a large Austrian-based producer of electricity) digital twins for hydropower.
“There’s been a transformation in operation of hydropower plants,” according to Alberts, “—an increase in renewable energy: wind and solar: [changes in] market mechanisms and price volatility, grid stability requirements, and climate change.”
A challenge for this company was fatigue cracks, which led to months of downtime.
The digital twin goals were to identify stress locations through virtual sensors and fatigue calculation for the critical component turbine; and a scaling solution to all Verbund hydropower plants.
The technical realization: a simulation model, sensitivity analysis, and digital twin generation, implementation in Verbund IT infrastructure, and IT infrastructure development to ensure operation of multiple digital twins, according to Alberts.
Next she brought up a use case of digital twins for a manufacturing company, naming challenges and realizations.
An initial challenge for the unnamed manufacturer was production efficiency and high operation costs. The solution was to optimize processes, and build a digital factory with automation.
“Digital twins simulate production processes, test various parameters without disrupting operation, and they optimize production flow, reduce waste, and minimize energy consumption,” Alberts says.
Other use cases involved a magnesium melting furnace at Rauch and valve manufacturing at Gemu.
To learn more about how to get from your company’s idea to a useful digital twin, click to view the full track.
In addition to the sessions described above, Bryan Pawlak of Goengineer provided an overview of configuring the right workstation for design and simulation, and Bob English of Valiant Products led a session on designing parts for additive manufacturing. You can register for the full on-demand Design & Simulation Summit here.
More COMSOL Coverage
More nTop Coverage
More TotalCAE Coverage
More Velocity Micro Coverage
Subscribe to our FREE magazine,
FREE email newsletters or both!Latest News
About the Author

DE’s editors contribute news and new product announcements to Digital Engineering.
Press releases may be sent to them via DE-Editors@digitaleng.news.
Related Topics
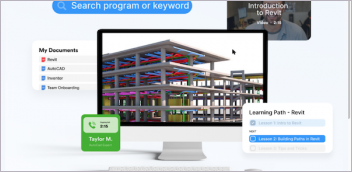
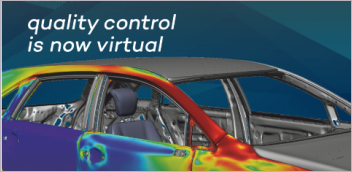
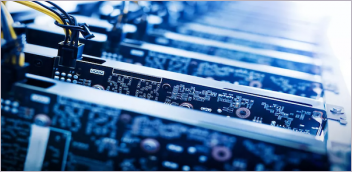
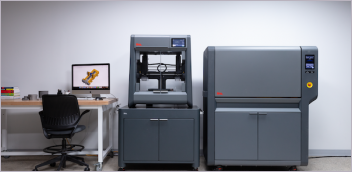