Winners of Altair Awards Are No Lightweights
Companies representing automotive industry share lightweighting recipes for success.

The primary lightweight concept for Nissan in Altair Enlighten Awards Full Vehicle runner-up category was intended to use common platform components, for example, seat frame, radiator, fuel tank and steering member, according to company officials. Image courtesy of Nissan.
October 7, 2020
Lightweighting is more than just a fleeting trend in the automotive industry. Employed properly in automotive manufacturing, it has the potential to lead to enhanced fuel efficiency, lower carbon emissions, streamlined aerodynamics and more. It's the result of design or materials modifications within the interior parts of a vehicle, such as the engine, chassis, etc. It's a significant enough approach that Altair annually highlights notable lightweighting achievements via its Enlighten Awards. This year's examples, hailing from big-name car and motorcycle manufacturers to automotive parts manufacturers were no exception.
Altair announced winners of its 2020 Altair Enlighten Awards back in August. The 8th annual awards, which are a collaborative effort with the Center for Automotive Research, represent the global best of the best in efforts to cut vehicle weight while still meeting/exceeding emissions goals, all in the name of sustainability. DE reached out to the winners to collect a behind-the-scenes perspective on the standout work from companies that earned accolades in this year’s competition.
The awards cover four categories: Full Vehicle, Module, Enabling Technology and Future of Lightweighting.
Full Vehicle winner, Harley-Davidson, used electrification to enhance energy capabilities in the electric motorcycle by 90%. Unfortunately, officials from H-D were unavailable for comment due to company restructuring.
So Full Vehicle runner-up, Nissan’s Tom Mally, associate chief vehicle engineer, Nissan Technical Center North America, stepped in to share details of its project, the new Sentra 2020 platform, built to enhance safety and performance without added weight.
Mally explains that the primary lightweight concept was intended to use common platform components, for example, seat frame, radiator, fuel tank and steering member.
“By applying these weight reduction ideas, we were able to achieve a lower and wider exterior design, provide enhanced dynamic performance and improved fuel economy and acceleration,” says Mally. “Compared to the previous generation Sentra, we were able to reduce approximately 100kg of weight, which then allowed us to add 200kg in performance improvement items.”
The 2020 Nissan Sentra was reportedly designed with safety and performance in mind—without added weight. The company's lightweighting approach opened up a lower and wider exterior design, as well as improved fuel economy, according to Tom Mally, vehicle engineer at Nissan Technical Center North America. Image courtesy of Nissan.
The project was not without obstacles though. Whenever common parts from a previous model are integrated into a new model, Mally explains, “a creative approach is required to incorporate them, while still providing a fresh and unique new vehicle.”
Another obstacle was the safety structure reinforcement. In the compact vehicle segment, Mally says it can be more difficult to absorb additional sheet metal weight compared to the proportions of larger vehicles. Nissan found it was necessary to use Ultra High Strength Steel (UHSS) mostly in the cabin area for a stronger passenger room. UHSS, according to Nissan, accounts for 30% of the metal usage to help offset as much of the weight increase as possible.
Looking back, Mally shares some tips for engineers who may be seeking creative ways to reduce weight in parts. He recommends evaluating the hot stamping process. “Utilization of the hot stamping process on key structural components can contribute not only to weight reduction, but also provide cost reduction opportunities. Hot stamping has very high strength and formability freedom,” Mally explains. These characteristics enabled Nissan to take complex shapes that are often constructed with a number of component parts in complex assemblies and cut down raw materials costs, stamping and assembly methods with use of thinner panels and combining into single, bigger parts.
Another household car name, Altair Enlighten Awards Module category winner, Toyota, built a freestanding two-person injection molded back frame without any molded reinforcement for its 2021 Sienna model. The project reduced 15 components down to one, lowering costs and mass and boosting safety.
Todd Muck, senior principal engineer Body Design for Toyota expounded on their company’s winning efforts. He credits Chief Engineer (CE) Monte Kaehr for the award-winning Lightweighting challenge for the 2021 Sienna.
“CE Monte wanted the lightweighting on the new Sienna to be directly beneficial and noticeable to the customer. For instance, in the seat back article … referenced, this lowers the effort to lift the seat substantially for the direct impact to the customer,” Muck says.
One of the greatest challenges for the Toyota team was temperature performance of the composite materials.
“The team had to rely significantly on the digital finite element analysis or computer-aided engineering for all temperature conditions that the vehicle may endure,” Muck explains.
It's fitting that there’s a saying at Toyota, “Start Your Impossible,” that, according to Muck, helps team members overcome its challenges. The resin seat back was the Seat Team’s “Start Your Impossible” moment, he notes.
Muck challenges engineers faced with lightweighting challenges to “push the status quo, push to make lightweighting without increasing cost. How can you make a design that improves mass, cost, and performance?”
For the Enabling Technology category, winner Mubea created a glass fiber-reinforced polymer Tension Leaf Spring that realized 75% weight savings, which would replace a traditional multi-layer steel spring.
The main advantages of this Tension Leaf Spring concept, according to Mubea officials, include the following:
- “extremely light” (up to 75% weight reduction)
- reduced unsprung mass
- increased payload capacity
- no rate transition during spring deflection
- no body frequency discontinuity
- no interleaf friction, which meant no noise or uncontrolled damping
- safe fail behavior
- improved lifespan, and
- reduction of assembly parts.
“The structural behavior of a [glass fiber reinforced plastic] Tension Leaf Spring is not only relevant in terms of component behavior (stiffnesses and durability) but also in its impact on the vehicle ride & handling performance,” reports Stefan Clemens, spokesman on behalf of Mubea.
“This lightweight product can easily be implemented in all rigid axle suspension systems, which mainly includes pickup trucks, light commercial vehicles (LCVs) and busses. The current potential worldwide market includes about 6M vehicles/year,” according to Clemens, who commented as part of a team involved with the project (Stefano Rosta, Mubea head of research & development, and Felix Beste, project manager of Customer Projects).
Looking back, Clemens says a key takeaway from the efforts for Mubea was not to substitute 1:1 steel by composite but to design a product by using the material’s properties.
Future of Lightweighting category winner, Marelli and its Ride Dynamics team specifically, have traveled a 10-year journey in the lightweighting space, having launched research projects with advanced metal alloys and composite materials along the way, according to Lisa Van Giesen, head of marketing and communications, North America, Marelli.
“We scouted, through benchmarking activities, different process technologies and materials in cooperation with academic partners and suppliers,” she says. “The goal was to find solutions to reduce weight, including identifying structural mechanical properties that could replace metal or be coupled with it.”
In the last decade, Marelli has homed in on metal replacement projects for the majority of its suspension product portfolio, having tested alternative materials for control arms, knuckles, subframe, twist beam axle and spring seat. The goal? To achieve functionality and lighter weight, according to Van Giesen.
“In addition, we have focused deeply on advanced sheet molding compression (ASMC) using carbon fiber sheet molding compound (CF-SMC) materials. We believe this to be one of the most promising technologies for structural suspension part design and manufacturing,” Van Giesen adds.
The advanced compression molded suspension steering knuckle—winner of the 2020 Altair Enlighten Award in the Future of Lightweighting category—does not represent Marelli’s first foray in ASMC process technology. “Encouraged by successful experiences with larger parts such as our suspension cross member (see figure 2), we further challenged ourselves to push technological limits and support complex structural SMC shape manufacturing,” she says.
More Altair Coverage
Subscribe to our FREE magazine,
FREE email newsletters or both!About the Author

Stephanie is the Associate Editor of Digital Engineering.
Follow DE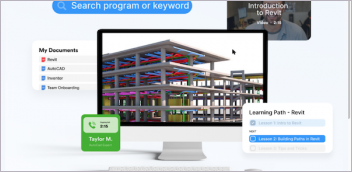
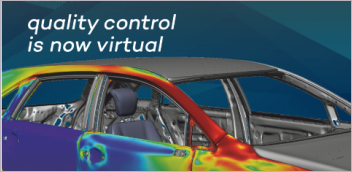
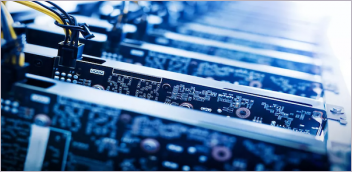
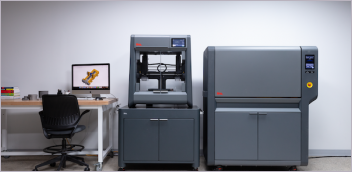