Latest News
May 31, 2021
Telework has become a crucial part of industry, which can be a stress point for manufacturing firms that were established around in-person collaboration and hands-on design validation. While many companies already utilize collaborative and simulation tools, the hardware and communicative needs of their tools and workflows often demand a specific standard for onsite workstations. Modern tools and technologies, however, can break down these previous limitations and help manufacturing companies increase efficiency while employees work remotely.
Simulation, cloud technologies, and virtualization are not new inventions They largely date back to the mid-1900s, but current advancements and pairings of these technologies provide opportunities and tools that, if utilized correctly, can greatly benefit the industry. Simulation tools such as Finite Element Analysis (FEA), Computational Fluid Dynamics (CFD), and Generative Design provide crucial information and contribute to a more efficient design process. By utilizing cloud services and virtualization, these tools can be optimized for both remote and onsite work.
FEA and CFD studies can replace the bulk of physical prototyping with rapid prototyping simulations. By converting 3D models into interconnected nodes (or points), a CAD program can model a variety of scenarios and reactions within simple parts and complex assemblies. These studies range from basic linear stress concentrations, natural frequencies, and impact tests to complex flow analyses. This approach can save a great deal of time and effort when prototyping. For example, designs can be tested nearly instantaneously compared to physical prototyping, and do not require onsite manufacturing and testing. The simulation workflow allows for continued feedback and modification of design, typically only requiring a physical prototype in the final phase.
With the benefits of simulation, it is no wonder that it is relatively commonplace in one form or another across the manufacturing industry. There is a reason, however, that remote work has been much less common until now. Even though these simulations can be run on most modern computers, there are thousands to millions of equations that need to be calculated by the computer to give meaningful results. Without the right hardware, this process can require hours or even days, especially for more complex studies such as CFD and Generative Design. For years these studies have been assigned to onsite workstations that can better handle the memory requirements than laptops and home computers.
Increasingly, the drawbacks of telework when using simulation can be mitigated using cloud-based tools and virtualization. Cloud services are commonly known for file storage and sharing but they can also be leveraged as a way to outsource heavy workloads to prevent taxing the local system. Cloud computing is a system built into some applications that allows advanced processes and studies to be run on a cloud server hosted by the developer rather than the local system. The study details are setup within the application and then submitted to the server via the internet to be processed. The study will continue to run even if the local system is turned off and the results can then be accessed by any computer with internet access by signing on to the appropriate account in the application.
Another easy way to boost the processing power while working remotely is using a Virtual Machine (VM). A VM is a virtual desktop hosted on a server by creating virtual hardware and allocating it to physical hardware on the server. By their nature, virtual machines have access to (or can be allocated) more resources than a laptop. The user simply logs into the VM from their computer over a network connection or the internet, depending on where the VM is hosted. This works in much the same way as remotely accessing an onsite workstation, except with the added benefit of not needing to maintain the individual workstation. While some companies prefer to host VMs on their own servers, cloud-based VMs allow the user to rely solely on their internet connection to access it rather than a less reliable network connection. Then, users can access their work from any computer with their credentials.
These different combinations and workflows can benefit a variety of companies across a wide range of industries and manufacturing methods. To better understand the diverse options, here are a few specific examples of simulation and cloud tools.
While designing custom injection molds a company may require validation and feedback on their cooling channels. If these channels were creating unwanted vortices or were too shallow, they would likely not be able to properly cool the mold leading to failed parts or increased lead times between injections. Autodesk CFD can be leveraged to validate the flow channels and analyze the flow pattern and transient heat transfer in the mold during the cooling process. While the studies will provide the necessary information, due to their complexity they are incredibly taxing on a local system and require extended run times to get meaningful results. By moving this tool to VM hosted by Workspot, the company can run the studies without burdening their local memory, freeing up their computer for other work while the simulation continues in the background on the VM. Beyond that the study could run at more than twice the speed than is possible on a remote workstation.
A different company interested in optimizing a series of legacy designs may use Autodesk Fusion 360 and take advantage of the cloud-based CAM application. This not only allows them the ability to collaborate on the designs simultaneously in an online space but also provides the power of Generative Design using cloud computing. The complex studies can be processed without using local memory or even overnight while the computer is off. Once completed the results are accessible for all team members to compare the results, study the stress analysis, and modify as needed. Once a design is selected, they could setup the CAM tooling and generate the G code to send to the manufacturer and begin production, all from remote workstations.
With the right tools for simulation, and remote work and collaboration, offices are no longer a requirement for efficient manufacturing. Design workflows built around Generative Design and simulation, with cloud and virtualization applications to support them, can quickly become the industry standard.
Tristan Gunderson is an Applications Engineer at M2 Technologies.
More M2 Technologies Coverage
Subscribe to our FREE magazine,
FREE email newsletters or both!Latest News
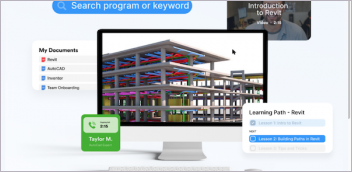
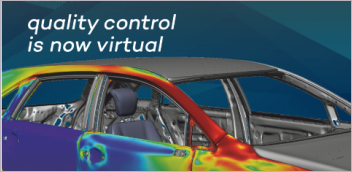
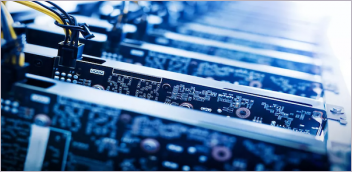
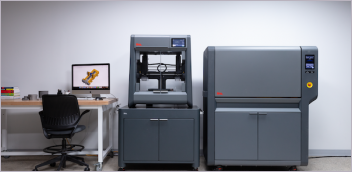