
Figure 1: In 2023, companies continued to deal with uncertainty stemming from lingering supply chain challenges, workforce dynamics, the continued growth of smart products, and more. Image courtesy of Siemens.
Latest News
January 23, 2024
With the start of the new year, it is time to look forward to how the trends and challenges of 2023 may change or persist into 2024. Last year, companies in all industries continued pressing through the uncertainty of recent history while also looking to a future of great potential. Market innovations have included the continued growth of smart and connected products in many industries as companies seek to improve functionality and user experience through software and electronics, and an increased interest in clean energy sources. Challenges related to supply chain management, workforce dynamics, and sustainable innovation drove the uncertainty of the last year while also offering key opportunities for innovation and creative solutions.
Cross-industry trends such as these are relatively stable and, as a result, the challenges faced by companies this year are much the same as before. That’s not to say that nothing has changed. Year-to-year differences, however subtle, do exist and will have large impacts on industries and companies in the coming year.
This year, I think about these trends in terms of the amount of pressure each is placing on industries, measured by an associated pressure gauge (figure 2). This allows us to examine each trend relative to the others and assess how it has changed over the last 12 months.
Five Pressure Gauges
Considering this set of pressure gauges, with one dedicated for each trend or challenge, we can think about how the readings on these pressure gauges will change from 2023 to 2024, and about what may be driving each change in pressure:
Workforce (Up): The challenges related to a changing workforce have not only continued, but also will grow more intense in 2024. The wave of retirees continues, leaving an acute need for engineers in the systems, electrical, and electronics domains. The next generation of engineers and technicians are arriving in industry with plenty of talent and passion, but not quickly enough to reinforce teams in need of resources. The result is that industries of all types are facing shortages in key roles, from engineering through manufacturing and beyond, leaving companies to find new methods of replacing outgoing talent and experience with a mixture of new talent and new technology.
Sustainability (Up): Companies are responding to multiple incentives and forces pushing industry toward a more sustainable future. These include new regulations, new business opportunities, and the ability to drive social change and establish positions of industry leadership in environmentally friendly operations. Moving forward, the pressure for companies to take action on climate change and improve the overall sustainability of their operations will continue to grow. Laggards will face significant penalties whether from various levels of government, lost business, or tarnished brand image.
Pace of Innovation (Even): There is a long trend of accelerating innovation cycles across many industries. This will not change in 2024 as companies are faced with faster development cycles and a constant drive to innovate to stay ahead of the competition. While this pressure is high, relative to other pressures, it will remain much the same into the new year.
Cost (Up): Things are more expensive at all levels of the supply chain. Producers face increased cost of labor and materials. On the consumer side, everything is becoming more expensive, which simultaneously reduces the consumer’s willingness and ability to bear any additional cost increases. The result is that companies are unable to increase prices to offset increased cost and must therefore seek to increase efficiency to manage cost and maintain their operating margins.
Supply chain (Down): Supply chain pressures have been relieved, particularly as silicon chip production has recovered. Even as this pressure gauge drops, companies must remain vigilant to the next disruption. There is no telling when or where the next disruption will occur, as was clearly demonstrated by the COVID-19 pandemic.
Figure 2: The major trends and challenges of recent years can be conceptualized as a set of pressure gauges, the readings of which indicate the intensity with which industries are feeling the effects of the associated trend or challenge. (Credit: Siemens)
How do companies get ready to take on the challenges of the future? It is critical to look beyond immediate fluctuations in industrial pressures and adopt a strategy to become more resilient, agile, and adaptive. The best way to do this is through digital transformation. Digital transformation enables companies to manage their businesses in both the real and digital worlds. This combining of real and digital unlocks a critical resource: data. Bringing these two worlds together enables the flow of data between all stakeholders involved in the development of a product or the production process itself.
Of course, every company generates lots of data. The real difference will become clear soon between the companies that simply seek to connect previously siloed data and those that endeavor to put that data to use, generating deeper insights and driving value for the business. Doing so enables companies to pursue higher levels of maturity in their digital transformation, enabling even more powerful capabilities.
A Holistic Approach to Digitalization
The success of a digital transformation program depends on more than just tools and technology, of course. The tools and technologies are critical, but how these tools are deployed, how the people within a company react to change, and how surrounding processes are adapted to help practitioners use the technology are equally as critical in realizing improvement. During COVID we saw companies react to a sudden and unexpected disruption by buying new tools that they likely did not need while passing on other tools they probably could have used. Even more detrimental, many of these companies never invested time or effort into understanding their new tool(s) or determining how processes needed to be updated to flatten the learning curve and extract the most value out of each tool.
Indeed, it is important to consider all these aspects to realize the full potential of digital transformation. Once a new tool has been identified that can drive a transformation in a process, the process needs to be optimized or redefined to take advantage of that tool, and the users need to be educated on how to effectively leverage that tool and the new process with continued support as they grow in their proficiency. Digitalization then expands throughout the company by repeating this activity: strategic implementation of new tools and processes and user education to accelerate adoption. Approaching a digital transformation strategy in this way will help companies become more resilient, adaptable, and ready to confront the disruptions of the future.
How do I know this process can help implement new digitalized solutions and achieve results? Because I have performed this process in my career. In a previous role I was part of a team developing an autopilot system for a commercial aircraft. Our main challenge was to design and develop this autopilot system while avoiding the costly process of in-air testing. Our solution was to build a digital model of the aircraft, complete with flight systems, aerodynamic properties, control systems, and more. We then integrated this model into a hardware-in-the-loop simulation with data collection hardware. This enabled our team to fly the aircraft virtually and collect critical data along the way, essentially creating a complete aircraft model and completing flight testing without ever leaving the ground.
Our initial goal was to reduce flight testing time for the autopilot development program by 66 percent. During the program, we achieved this and more, ultimately completing our testing program with an 85 percent reduction of flight-testing time. What’s more, through continued learning and development of the tool and process, we were able to create a high-fidelity flight simulator that enabled us to evaluate aircraft concepts and designs before they existed in any physical manner. There is no doubt that this required immense effort and investment, but it was also a novel approach at the time that resulted in a huge return on investment. Today, such approaches are essential to the development of the complex, intelligent products of tomorrow.
Encouragingly, technology partners such as Siemens can offer much more powerful solutions along with industry experience and technological expertise to kickstart digital transformation and support companies along their journey.
Of course, technology plays a key role in enabling digitalized solutions to tomorrow’s challenges. Artificial intelligence (AI) will be critical to increasing the processing speed and throughput of data, which will enable accelerated product and process evaluation and innovation. Today, AI can help automate mundane tasks, leaving engineers more time to focus on solving design challenges. In the near future, the capabilities of AI will prove even more impactful as they will provide the foundation for the highest level of digital transformation maturity.
In the production space, the convergence of information and operation technologies (IT/OT) will provide greater flexibility and visibility, empowering manufacturers to make highly informed decisions through real-time process monitoring of the shop floor. IT/OT convergence enables managers to easily assess the business impact of manufacturing activity, and it supports and encourages collaboration across planning, scheduling, and factory performance, leading to superior efficiency.
2024 and the Digital Transformation Journey
While digital transformation can help companies address the more immediate pressures coming in 2024, it can offer much more to companies that build a plan to evolve beyond connecting data into higher level functions such as automation of data management and eventually the closed-loop optimization of products and processes. In fact, I think of digital transformation as a journey that includes five major milestones (figure 5): configuration, connection, automation, generative design, and closed-loop optimization.
Leaders in digital transformation today are generally entrenched in the first two stages of this process of maturation. These stages are configuration, or the switch from a document-based to a model-based data framework, and connection, which focuses on breaking down silos that isolate model-based data. These two stages vastly improve the traceability and accessibility of data throughout the organization, helping to increase process efficiency, improve engineering flexibility, and enhance results even on aggressive project timelines.
Such benefits are worth celebrating, but insufficient relative to the pressures companies continue to face. Higher levels of digital transformation maturity do more than unlock a company’s data; they employ advanced technologies to put that data to work as a force multiplier for engineers, industrial planners, technicians, and more.
Figure 5: The digital transformation journey includes five key maturity milestones.
The third level involves the automation of tasks, starting with the mundane and progressing to more and more complex operations that, so far, only humans have been able to perform. These higher forms of automation will rely on AI to transform engineering and other processes. The role of AI will continue to grow throughout the digital transformation journey. The fourth level, generative design, further leverages the capabilities of AI to generate designs of products, manufacturing processes, and other artifacts in line with a company’s design history and based on user inputs.
In this context, generative design is used to refer to a broader set of capabilities than those available in software packages today. Rather than optimizing the physical geometry of a single component, AI-powered generative design can work across domains to integrate varied sets of requirements and optimize the performance at a system level. This will certainly begin with subsystems before building to the cross-domain generation of an entire advanced product.
The final stage implements this generative design technology in a closed-loop process of generation, evaluation, iteration, and selection of an optimized design. AI will generate thousands of designs for a product or system, evaluate these designs against various requirements, and select the design or designs with the highest performance. These selections would be reviewed by a team of human engineers to ensure quality and make the final selection for refinement and, ultimately, production. Such capabilities will enable teams of dozens of engineers to achieve what would have once required hundreds or thousands of engineers.
To reiterate, digital maturation is a process that companies should begin with a plan and a long-term perspective. The minutiae of this journey will vary from company to company and overcoming day-to-day challenges will require agility and strong partnerships throughout the industrial ecosystem. Companies that embrace this journey will not only overcome the challenges and pressures of 2024, but surge ahead of the competition as they move faster and more efficiently while building advanced and intelligent products and processes.
Dale Tutt is the Vice President of Industry Strategy for Siemens Digital Industries Software, leading the development of digital transformation solutions that address the industry-specific needs of customers. Tutt joined Siemens in 2019 as the Vice President of the Aerospace and Defense Industry. Prior to joining Siemens, Tutt worked at The Spaceship Company, a sister company to Virgin Galactic, as the VP of Engineering and VP of Program Management, leading the development of spaceships for space tourism. He led the team on a successful flight to space in December 2018. Previously, Tutt worked at Textron Aviation/Cessna Aircraft in program and engineering leadership roles. As the Chief Engineer and Program Director of the Scorpion Jet program, he led a dynamic cross-functional team to design, build and fly the Scorpion Jet prototype from concept to first flight in 23 months. Tutt also worked as an engineer at Bombardier Learjet and General Dynamics Space System Division.
More Siemens Digital Industries Software Coverage
Subscribe to our FREE magazine,
FREE email newsletters or both!Latest News
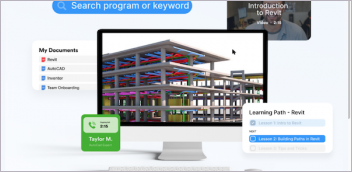
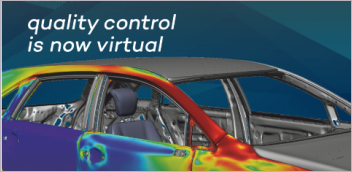
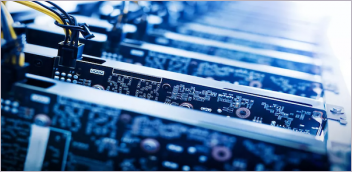
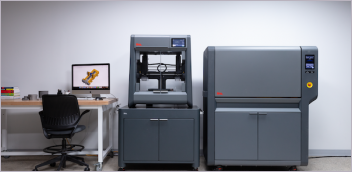