Minimally Invasive Surgery with 3D Printed Suturing Device
Despite its advantages, minimal invasiveness in surgery is impeded by a lack of specialized instruments suitable for such detailed and delicate tasks.

Sutrue’s device machined from steel
Additive Manufacturing News
Additive Manufacturing Resources


Boston Micro Fabrication

May 16, 2023
While recovering from a broken ankle in 2008, Alex Berry, Founder and Engineering Director of Sutrue, first came up with the idea of an automated suturing device for minimally invasive surgery.
Minimally invasive surgery offers patients reduced recovery times, better outcomes, and fewer complications. However, the limited availability of instruments suited for this type of small and very precise task impedes the surgeon’s abilities to offer their patients minimally invasive options.
Sutrue’s minimally invasive suturing device is designed specifically in mind for keyhole surgery – both laparoscopic and robotic. Suturing is one of the fundamental duties of surgeons, and yet there is not instrument available that enables their performance on the scale necessary for minimally invasive (8mm diameter). Sutrue’s innovative design addresses this gap, and the small size of the prototype devices require extreme accuracy.
Suturing for Minimally Invasive Surgery
After years of research and experimenting, Berry’s team designed a device that operates by passing a suturing needle and thread through tissue and returning into the device securely. The needle rotates out and back into the device on a fixed path while staying level on the third axis. The team had prototypes of the device machined from steel, which required a significant amount of time and could not easily accommodate design iterations.
Prototyping the Device
While developing the suturing device, Berry’s team needed to update one of the most important device components, relating to the stability of the needle’s path. Machining the part again would have delayed testing the product by several months and cost a significant amount of money. Machining also left no room for experimentation as the team would only be able to receive one replacement design.
3D printing the replacement parts allowed the team to test different versions of the part with small differences to test various tolerances in a short timeframe. Additionally, working with 3D printing also allowed the team to consider aesthetics, having the parts printed in two different colors.
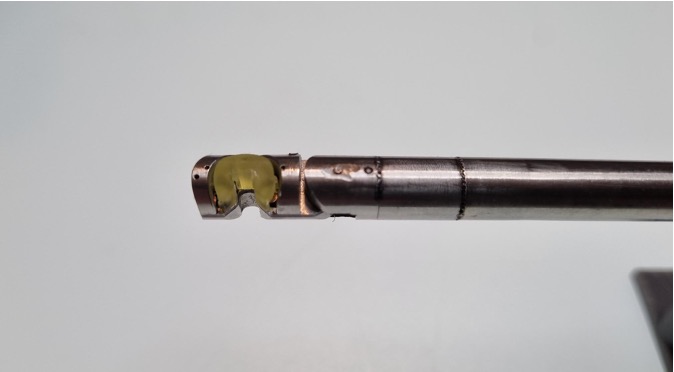
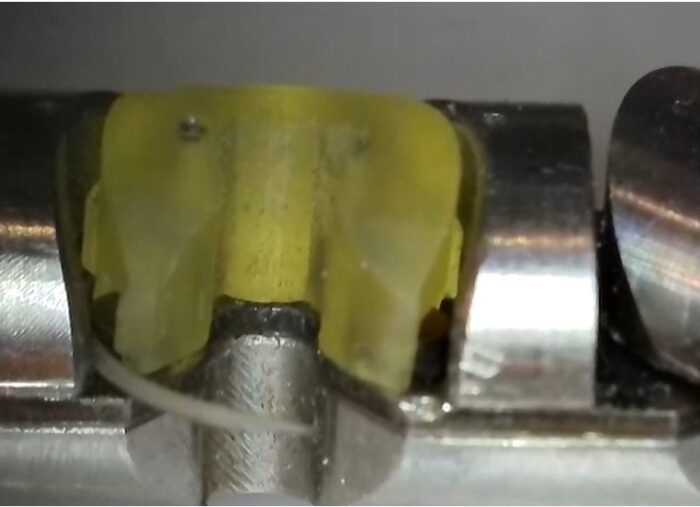
Alex Berry, Founder and Engineering Director at Sutrue:
“The accuracy of BMF printers at small scale means that we could try three different parts to find the ideal fit. This allowed for our device to finally function as designed without the cost and time delay of machining the part. This has led to us being able to do initial testing and advance the development of a unique medical device with the assurance that the BMF printed parts are true to the design and consistently accurate.”
Continuing Advancements for Minimally Invasive Surgery
Advances in medical devices will continue to expand the availability of minimally invasive surgery. The ability to 3D print prototypes at the resolution, size, and tolerance of precision injection molded parts opens up the possibilities for advancements in the instruments required for minimally invasive procedures.
To learn more about micro 3D printing applications for instruments needed for minimally invasive surgery, contact BMF.
More Boston Micro Fabrication Coverage
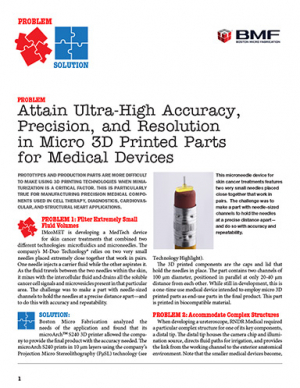
Subscribe to our FREE magazine,
FREE email newsletters or both!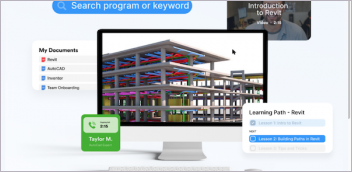
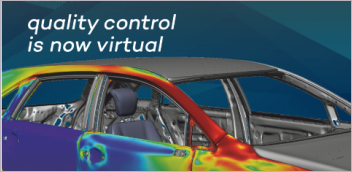
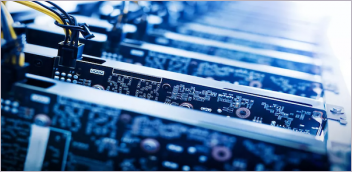
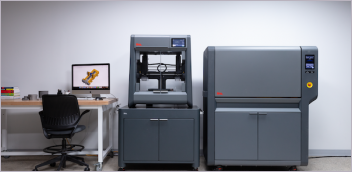